Fuse Recruitment's Safety Hub
Your Safety, Our Priority – A Comprehensive Guide for Staying Safe on the Job
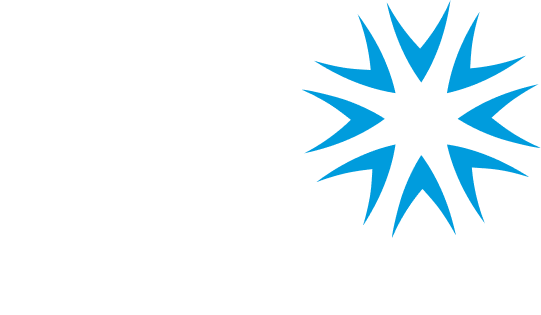
Welcome to the Fuse Safety Hub!
Welcome to the Fuse Safety Hub – your go-to resource for staying informed and proactive about workplace safety.
We're committed to building a safety-first culture, helping to minimise risks and ensuring that every shift ends with you returning home safely.
This page is regularly updated, so feel free to check back whenever you need the latest information.
Remember, safety is a team effort, and your role is crucial in creating a safe environment for everyone.
If you ever have questions or concerns, don’t hesitate to reach out to your Fuse Consultant – we're here to support you
Promoting a Safety-First Mindset
Safety isn't just a policy - it’s a mindset that we bring to every job, every task, every day.
We’re committed to creating a Safety-First culture where we and every member of our workforce, including you and your employer, actively prioritises safety at work.
Hazards can arise at any moment. That's why it's crucial that safety is always top of mind. A safety-first culture means:

Safety is the foundation of a successful career, especially in high-risk environments. We are dedicated to ensuring that every worker feels safe, supported, and empowered to perform their role with confidence. Here's how we uphold that commitment:

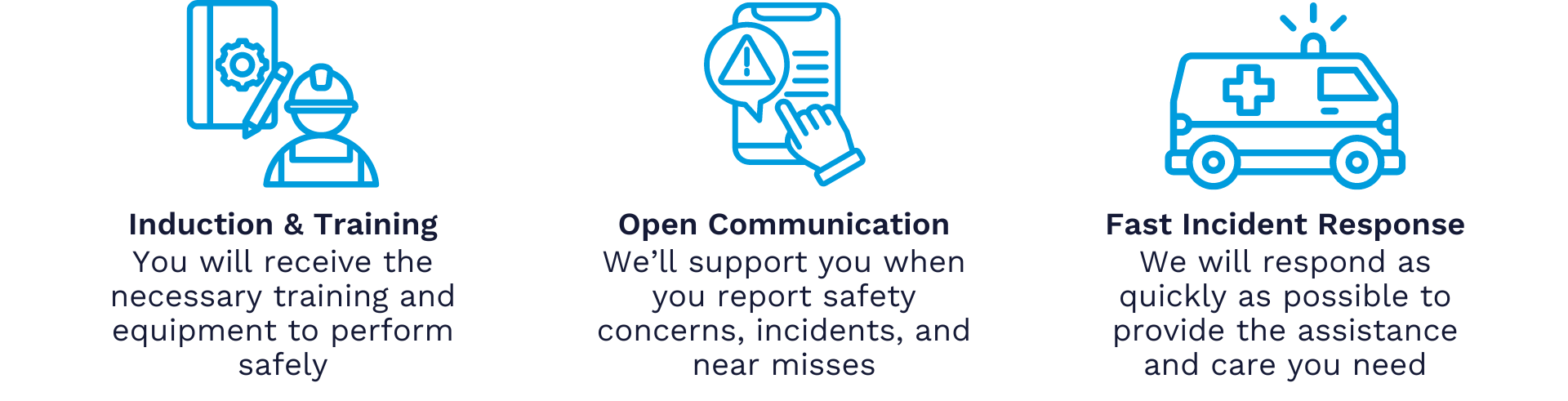
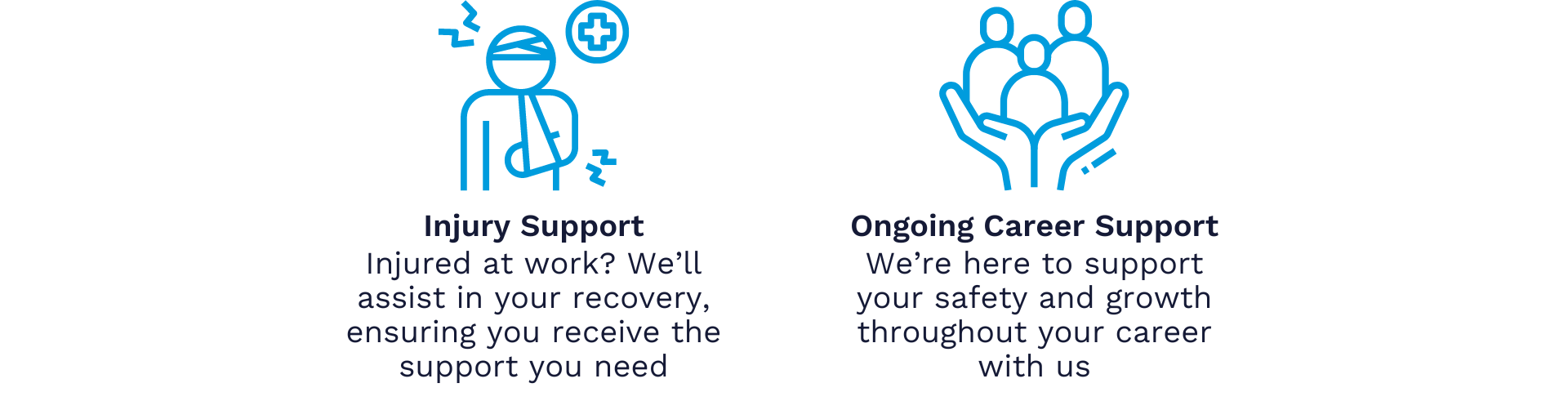
Your contribution is vital to our safety culture. Here’s how you can help:
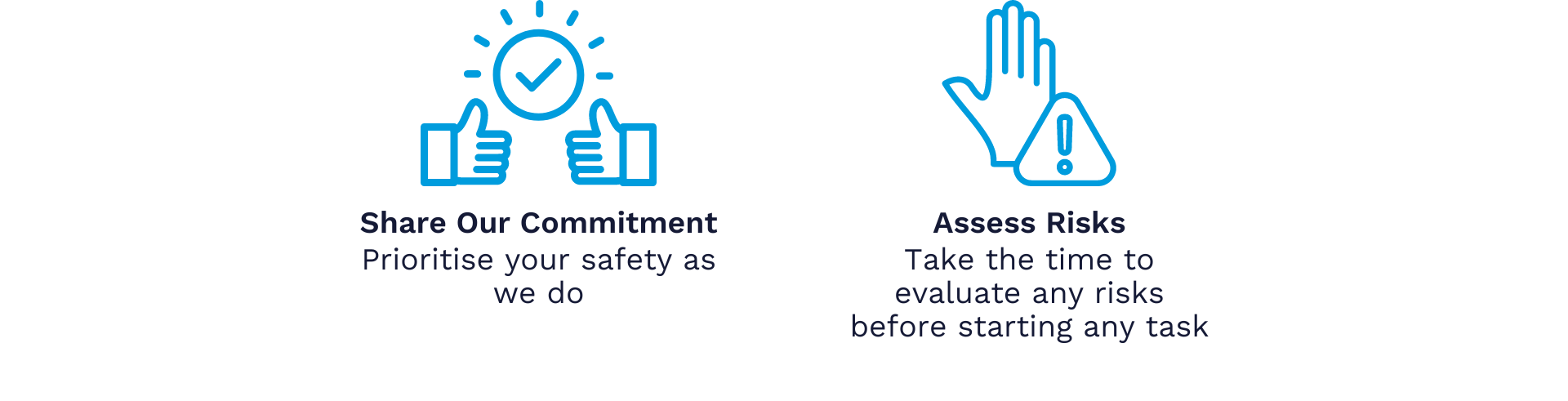
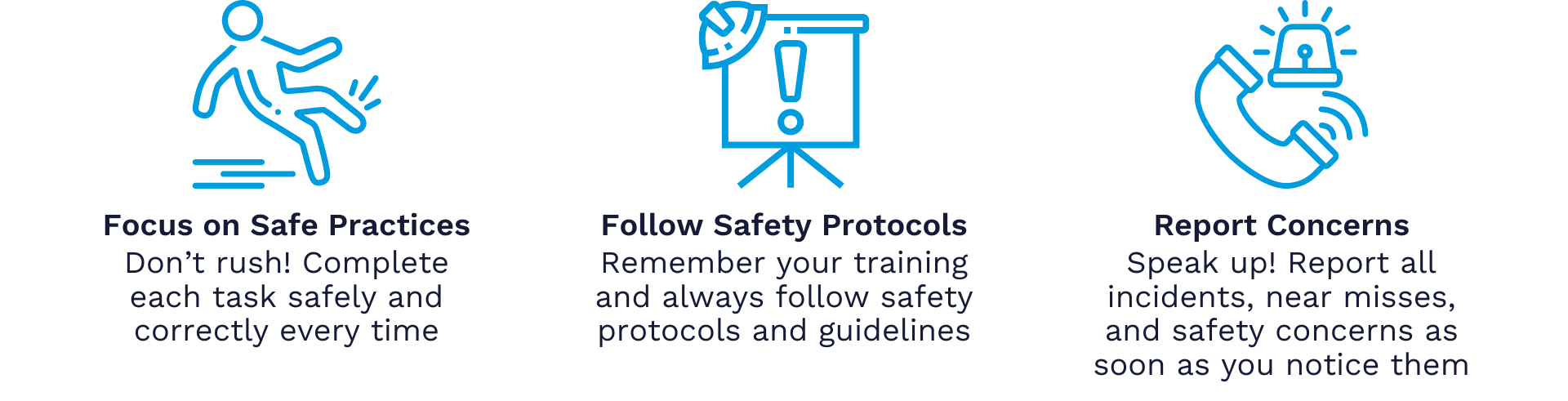
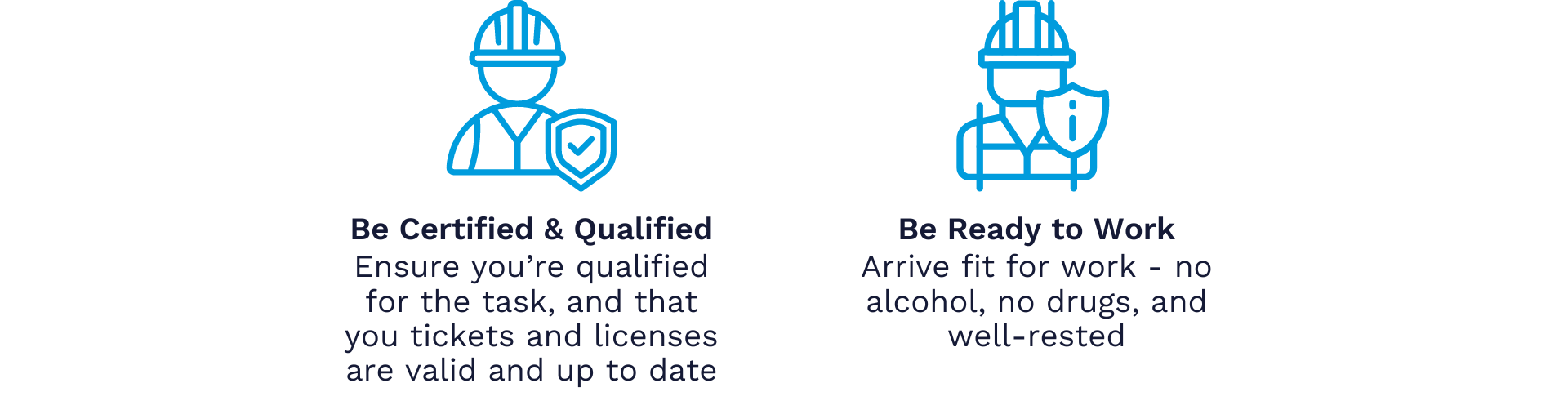
By embracing a Safety-First mindset, you’re not just protecting yourself - you’re contributing to a safer work environment for everyone. When safety is front of mind, we reduce risks and ensure that everyone returns home safe at the end of each shift.
Incident Reporting
What to do if you are involved in an incident at work
- 1.Ensure Immediate Safety
If an incident occurs, the first priority is your safety and the safety of others. Move away from immediate danger, secure the area, and attend to any injured persons if it's safe to do so.
- 2.Seek Medical Attention (if necessary)
If anyone is injured, seek medical help immediately. Administer first aid if you’re trained to do so, or contact emergency services for serious injuries.
- 3.Notify Your Supervisor or Manager
Report the incident to your supervisor, manager, or safety officer as soon as possible. Ensure they are aware of the situation so they can take the necessary steps to investigate and resolve it.
- 4.Report Near Misses, Hazards and Incidents
Even if an injury didn’t occur, report near misses and potential hazards to prevent future accidents. Click here to report an incident.
- 5.Cooperate with the Investigation
Be available to answer any follow-up questions or clarify details during the investigation of the incident.
- 6.Follow Up on the Outcome
After reporting the incident, follow up to ensure that corrective actions have been taken, and learn from the situation to prevent similar incidents in the future.
By following these steps, you ensure that incidents are managed efficiently and effectively, contributing to a safer work environment.
Why Reporting Incidents Matters
Your safety is our top priority, and reporting incidents is a crucial part of keeping everyone safe. Whether it’s a near miss, minor injury, or something more serious, letting us know about it helps prevent future accidents.
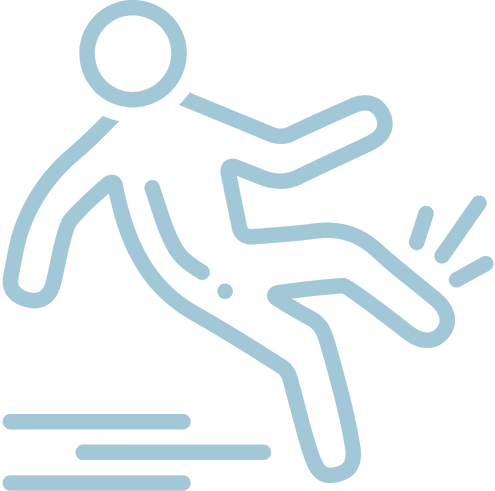
Prevent Future Accidents
Reporting incidents gives us the chance to fix hazards before they cause harm. Your quick action can protect you and your coworkers.

Speaking up is safe, and we’ll stand by you
We want to be clear—reporting an incident won’t get you into trouble. We value transparency and will always support you when you speak up about safety concerns.
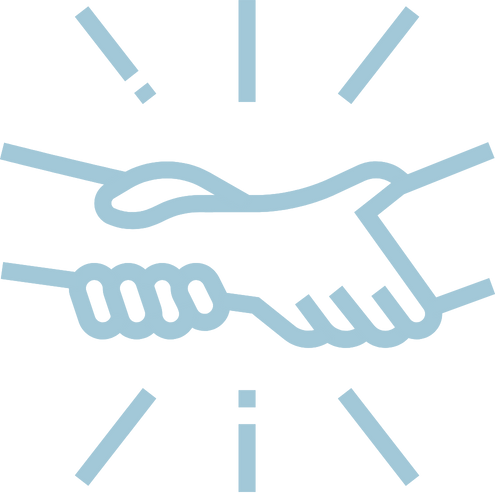
Our Support
When you report an incident, we’ll act quickly to investigate, address the issue, and provide the help you need. Your safety comes first, and we’re here to make sure you feel secure in doing your job.
By reporting incidents, you’re helping create a safer workplace for everyone, and we’ll stand by you every step of the way.
Your Safety On the Job
Ensuring Safe Equipment Operations
Whether you’re handling heavy-duty machines or everyday tools, following the proper guidelines is crucial to preventing accidents. Always follow these key guidelines:

- Proper Use: Ensure you're trained and authorised before using any equipment. Always read and follow the manufacturer's operating instructions carefully
- Regular Maintenance: Regularly conduct proper maintenance to ensure equipment is in working condition and does not become a hazard
- Check for defects before use: Check your equipment before you use it to ensure it’s in good working condition. If you notice any defects, report them immediately and avoid using faulty equipment until it’s repaired
- Right Tool for the Job: Use the correct tool or machine for each task - don’t improvise. This helps prevent accidents and damage to equipment. Make sure you’re always equipped with the appropriate tools and know how to use them correctly
By handling equipment with care, you minimise risks and maintain a safe work environment.
Approaching High-Risk Tasks with Confidence
High-risk tasks - such as working at heights, in confined spaces, or handling hazardous materials - require an elevated level of awareness and precaution. Ensuring your safety in these situations means strictly adhering to safety protocols and being fully prepared for the task ahead. Here’s what you need to keep in mind:

- Proper Training: High-risk tasks require specific training and certifications. Before engaging in any high-risk work, ensure you’ve completed the necessary training to handle the task safely and competently. If you’re unsure about any part of the job, ask for additional guidance or training
- Use the Right PPE: Personal protective equipment (PPE) is your first line of defence in high-risk environments. Whether it’s a helmet, harness, gloves, or respirator, make sure you’re wearing the appropriate PPE for the task and using it correctly
- Follow Protocols: High-risk work follows strict safety protocols to protect you. Always follow established safety procedures, no matter how routine the task may seem. These protocols are in place to minimise danger and ensure the safe completion of the job
By preparing thoroughly and following safety guidelines, you help prevent accidents and protect yourself and others during high-risk tasks.
Adapting to Environmental Challenges
The conditions you work in - whether it’s the weather, noise, or airborne particles like dust - can present unique safety challenges. Being aware of and adjusting to these environmental factors is important to maintaining a safe and healthy work environment. Here’s how to stay safe:

- Weather Awareness: Weather can change rapidly and impact safety on the job. In hot conditions, stay hydrated and take breaks to prevent heat exhaustion. In cold or wet environments, dress in layers and protect yourself from the elements to avoid hypothermia or slips
- Noise Control: Long-term exposure to loud environments can cause hearing damage, even if you don’t notice it immediately. Use ear protection, such as earplugs or earmuffs, in noisy work areas to reduce the risk of hearing loss over time
- Dust Management: Working in dusty environments can impact both your respiratory health and visibility. Use proper ventilation, safety goggles or wear masks to limit dust exposure. Keeping your workspace clean and free from excessive dust also helps maintain a safer environment
By staying vigilant and adjusting to environmental challenges, you ensure not only your own safety but also the safety of your team.
Alcohol and Drugs: Fit for Work, Every Shift
Your safety and the safety of those around you depend on being alert, focused, and fit for work. That’s why it’s critical to be free from the influence of alcohol, drugs, or any substances that can impair your judgment or reaction times.

- No Alcohol or Drugs: Arrive at work sober and clear-headed. Even small amounts of alcohol or drugs can slow your reflexes and affect decision-making. Being under the influence at work puts you and your colleagues at risk
- Prescription Medications: If you’re taking medication that may affect your ability to perform your job safely, let your supervisor or Fuse Consultant know before you show up to work. It may be unsafe for you to perform your usual tasks or be onsite. Your safety is the priority
- Zero Tolerance: We have a zero-tolerance policy for drugs and alcohol in the workplace. Being under the influence puts everyone at risk and will lead to disciplinary action
By staying sober and alert, you help create a safe environment where everyone can work confidently and return home safely.
Every Workplace is Different, Get to Know Yours
Every workplace and job has its own unique safety protocols. Understanding the specific safety measures, emergency procedures, and standards in your work environment is essential for handling both routine tasks and unexpected situations.
Here are cases where your workplace's safety guidelines may differ to others:

- Emergency Procedures
Familiarise yourself with the evacuation routes, emergency exits, and locations of first aid kits and fire extinguishers. Make sure you understand your role in an emergency and participate in any drills or training sessions. - Workplace Safety Standards and Job-Specific Training
Each job has safety standards specific to the work you perform. Whether it’s machine guarding, proper lifting techniques, or wearing the right PPE, these standards are designed to keep you safe from job-related hazards. If new safety guidelines or equipment are introduced, make sure you’re informed and trained properly before using them. Take the time to learn the safety protocols specific to your tasks, and don’t hesitate to ask questions if anything is unclear.
Take ownership of your safety by getting to know the details of your workplace’s safety protocols.
Your Health and Wellbeing
Staying Safe and Healthy at Work
Your health - both physical and mental - plays a big role in staying safe on the job. Here’s how you can manage fatigue, reduce stress, and stay physically prepared for work:

Fatigue Management
Fatigue can be just as dangerous as any physical hazard. Take regular breaks, get enough rest between shifts, and manage your workload to avoid burnout. If you're feeling tired, speak up - it's better to slow down than risk an accident.

Mental Health Support
Stress and mental health can impact your safety and performance. If you're feeling overwhelmed, know that help is available. To ensure you're supported both on and off the job, Fuse has partnered with EAP Assist; Australia's leading Employee Assistance Program provider with immediate confidential counselling support & advice services.
Browse EAP Assist's library of support articles here.

Physical Health Tips
Taking care of your body helps prevent injuries. Stay hydrated, follow proper ergonomic practices, and take time for stretches or light exercises to avoid strain, especially during repetitive or physically demanding tasks.
By managing your overall well-being, you contribute to a safer, healthier workplace - for yourself and your team.
Employee Assistance Program
At Fuse, we care about the health and well-being of our workers, which is why we offer our Employee Assistance Program (EAP) to our on-hired workforce.
What is an Employee Assistance Program?
The EAP is a service that allows you to safely and confidentially discuss any psychological distress you may be experiencing. The issues you discuss don't need to be work-related, you are welcome to use this service for anything, and we encourage you to make the most of it. EAP Assist is independent of Fuse, and we have no visibility on who is using it, or what they are using it for.
How to access EAP Assist:
- Call the Fuse helpline on 0407 086 000
- Make an online booking with a counsellor
- Email support@eapassist.com.au
Please note that the EAP is not a replacement for any OH&S obligations you have. If you have an incident at work, you are still required to report it to Fuse and your host employer.
If you have any questions regarding the use of the EAP, please ask your Fuse consultant.
Additional Resources
Incident Description
The worker was moving products with a vacuum lift. The lift was disengaged when the product was not in alignment with the location of the release. The product missed the pallet and fell on the leg of the worker.
Injury / Near Miss
Minor bruising to foot.
Action Taken
Medical assessment and treatment. Assessment of root cause of incident and communication to workers to "take 5" and ensure the task is completed correctly.
Prevention
- Ensure that all staff understand the importance of following directions
- Ensure that all lifting equipment is correctly maintained to eliminate any issues
Incident Description The worker was walking down a steep slope after a rain event carrying a winch from a truck to the location of work and twisted their knee due to the slippery surface. Injury / Near Miss Left medial collateral ligament sprain. Action Taken A full injury management process was undertaken and a stop-work was enforced on site due to the Hazard and inability to prevent further accidents from occurring on the day. Prevention
- Ensure workers have appropriate footwear - e.g. Laced up steel-capped non-slip boots
- Minimise changes in floor levels - e.g. if levels must change, use steps and provide handrails when applicable or, change the location of the truck to lessen the distance of manual carrying
- Provide a trolley or other mechanical aid to carry objects
Incident Description The worker was entering into work premises from the car park and about to ascend the stairs when they stumbled, landing heavily and fracturing their arm. Injury / Near Miss Fracture to the right forearm. Action Taken Review of incident and location where the incident occurred to ensure walkways were suitable, and clear of any obvious slip or trip hazards, with adequate lighting and handrails. Communication to all workers to be aware of their surroundings when moving on site, not to walk and look at a phone, use handrails etc. Prevention
- Ensure all staff have suitable footwear
- Communicate to all workers regularly the importance of being aware of surroundings, slip and trip hazards and correct usage of stairs
Incident Description
The Employee was walking backwards not watching his surroundings and fell backwards into a truck service pit.
Injury / Near Miss
Torn ACL, ruptured PCL.
Action Taken
Markings around the service pit were repainted, barriers were raised, and multiple people working around the area.
Prevention
- Ensure staff are not walking backwards in this environment
- Grates were added to the front of the service pits to be closed when no one operating in them
- All staff retrained that work in that area
IMS
Fuse Recruitment specialises in temporary and permanent staffing recruitment solutions in the Manufacturing, Infrastructure, Utilities, and Insurance and Wealth Management Industries.
Our company strives to achieve sustainable growth by consistently satisfying the diverse needs and expectations of our clients. Fuse Recruitment, through its executive management team, is committed to the effective implementation of the Integrated Management System (IMS) in compliance with ISO 9001 Standard and ISO 45001 Standard.
Top Management is committed to:
- Taking overall responsibility and accountability for the prevention of work-related injury and ill health as well as the provision of safe and healthy workplaces and activities;
- Ensuring that the IMS policy and related IMS objectives are established and are compatible with the strategic direction of the organisation;
- Ensuring the integration of the IMS management system requirements into the organisation’s business processes;
- Promoting the use of a process approach and risk-based thinking;
- Ensuring that the resources needed to establish, implement, maintain and improve the IMS management system are available;
- Communicating the importance of effective IMS management and of conforming to the IMS management system requirements;
- Ensuring that the management system achieves its intended outcomes;
- Directing and supporting persons to contribute to the effectiveness of the IMS management system;
- Ensuring and promoting continual improvement;
- Supporting other relevant management roles to demonstrate their leadership as it applies to their areas of responsibility;
- Developing, leading and promoting a culture in the organisation that supports the intended outcomes of the IMS management system;
- Protecting workers from reprisals when reporting incidents, hazards, risks and opportunities;
- Ensuring the organisation establishes and implements processes for consultation and participation of workers;
- Support the establishment and functioning of health and safety committees,
- Eliminate hazards and minimise OH&S risk using the hierarchy of control
The company strives to achieve this by:
- Identifying and managing risks and opportunities to meet the expectations of employees, contractors and customers;
- Promoting an understanding of our customers’ needs and expectations throughout the organisation, together with a culture of exceeding customer expectations;
- Aligning the purpose and context of the organisation and supporting its strategic direction through stakeholder analysis;
- Ensuring compliance with all applicable legislation, regulations, customer and other relevant requirements;
- Ensuring the wellbeing of an employee in the event of an incident or injury and supporting a safe and early return to work;
- Applying learnings from incidents to prevent recurrence with the aim to eliminate injury and illness;
- Developing seamless processes by fully integrating the services we provide;
- Monitoring our performance through performance metrics (e.g., internal audits) in order to continually improve our processes and services;
- Ensuring that management on all levels communicates and explains the IMS policy to all employees so that everyone is familiar with the policy and its intent. It is also made available to interested parties;
- Reducing, as far as reasonably practicable, non-conforming products or services;
- Establishing, reviewing and communicating the company’s safety, quality and business performance against objectives and targets, to all levels in the organisation. The objectives are monitored on an ongoing basis through the quality management plan and reviewed during planned management review meetings
Approved by: Mathew Westcott
Position: Managing Director
Date of Initial Approval: 28 August 2016
Date of Version 4 Approval: 5 June 2023
Date of next review: 18 May 2024
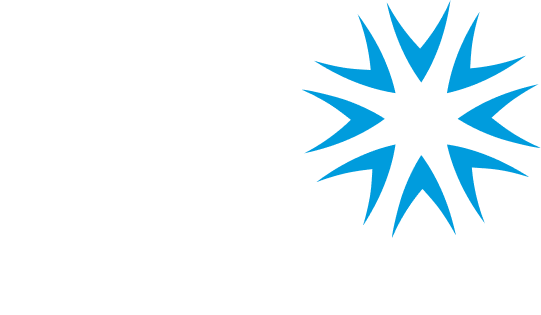
Our Values
